A case study on the corrosion of a cold-stacked ageing Jack-up drilling rig
INTRODUCTION
Corrosion costs billions of pounds every year in the Oil & Gas Industry. Mobile Offshore Drilling Units (MODU) are subjected to high risk of corrosion due to varying temperature and high salinity of seawater. Besides, cold stacking of a jack-up, especially an aged one, might lead to deterioration due to corrosion if a reasonable corrosion control system is not in place and the cost of repair might be much higher than keeping it warm stacked. In this case study, we present the high deterioration within the pre-load tanks after cold stacking based on our experience when working as supervisors for the survey and repair of a jack-up.
JACK-UPS
A jack-up is a Mobile Offshore Drilling Unit (MODU) which consists of three main components including Hull, Legs and Spudcans as well as equipment as shown in the Figure below:
The Hull is a watertight structure on which Cantilever and Jacking System, living quarter, Helideck and the equipment are housed. The leg and spudcans are steel structures which support the hull when the hull is elevated. The spudcans of the jack-up are footings that sit on seabed and increase the legs bearing area.
COLD AND WARM STACKED
Warm stacking of a jack-up is that the rig is not in operation but is kept running with engines and lights on with a fewer crew. The rig would be ready to be operational in a short period. In contrast, cold stacking is when the engines are off and only temporary lightings working for conducting checks. There is no crew on board and only a few security staff are working, hence the rig is idle. The rig is usually cold stacked when there is no expectation of operation in a short period; hence, reducing the financial cost of warm stacking. However, if a cold stacked rig is not reasonably preserved, it will deteriorate and corrosion might be a big problem and quite expensive to re-activate. This is a bigger problem with older jack-ups.
CONTROLLING CORROSION
The two principal methods of controlling corrosion are Protective Coatings and Cathodic Protection. Both methods are used in conjunction with each other on jack-up rigs to mitigate the corrosion.
Coatings
To control corrosion, protective coatings are used for different parts of jack-ups. In applying such coatings, the lasting protection, easy to apply and cost-effectiveness, abrasion resistance, resistance to corrosion chemicals, water and heat resistance, durability and environmental need to be considered.
Cathodic protection
Jack-up legs are made from high strength steel with the yield strength of up to 700 MPa. Corrosion fatigue might occur due to deterioration of steel due to corrosion. To prevent the steel on jack-up rig legs from corrosion caused by seawater, a cathodic protection system is usually used. There are two types of cathodic protection systems.
A simple method for Cathodic Protection is to weld sacrificial anodes on the rig legs and spread them evenly around the whole leg. The anodes are blocks of metal which will corrode faster than steel, for example, zinc or aluminium. Thus the steel will be protected from corrosion when the anodes are connected directly to the steel.
Impressed Current Cathodic Protection (ICCP) is another way to protect underwater steel structures from corrosion. The working principle of the system is based on feeding a controlled amount of DC over the steel structure. Anodes and reference cells connected to a control panel are mounted on the steel. The current produced by the system is more powerful than the natural electrochemical activity on the steel surface, and that activity can, therefore, be suppressed and spare the steel from corrosion.
CORROSION TEST METHODS
Visual Inspection has been the primary method to assess corrosion damage on the surface of the metal. However, it is very dependent on the experience of the inspector. This method will not detect surface discontinuities.
Non-Destructive Testing (NDT) is a technique used in the number of industries to detect and evaluate the properties of the material and to test for any internal defects and flaws. It can also be used for measurement of the thickness of the material. There are several techniques for Non-Destructive Testing. Ultrasonic and magnetic particle inspection are among two common NDT methods and presented briefly as follows:
Ultrasonic Testing (UT) In this method a sound wave is sent into the material and its interaction with the material is observed. It can be used for the corroded parts which are inaccessible for visual inspection.
Magnetic Particle Inspection (MP) It is used for detecting surface and near-surface discontinuities by magnetising the material. A sensor will detect the magnetic flux leakage that is generated around the flaws such as cracks.
Case Study
The jack-up rig studied in this paper was constructed in 1985 with a maximum water depth of 328 ft. The authors had the opportunity to supervise the survey and repair. The rig was cold stacked for a year and the initial survey showed that the corrosion was the main part in the integrity management of the rig and has to be dealt with in the repair.
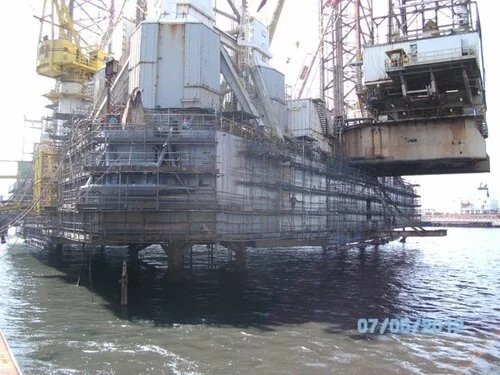
Hull perimeter before the protective coating
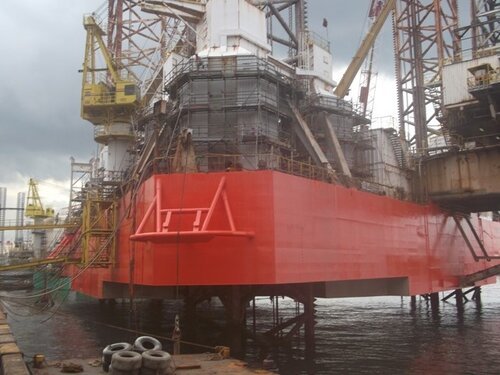
Hull perimeter after the protective coating
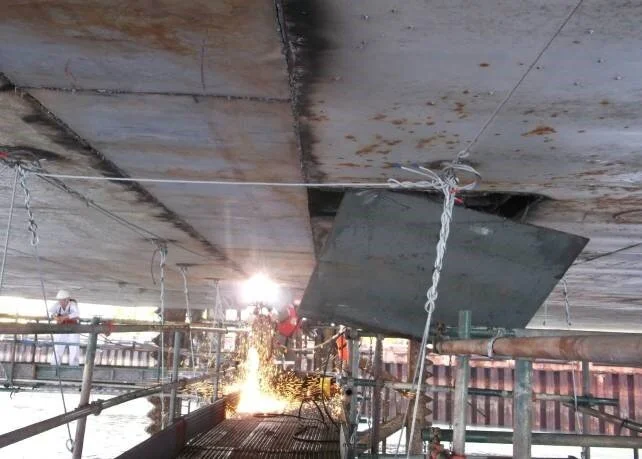
Holes identified in the bottom of the Hull during integrity check and the steel renewed
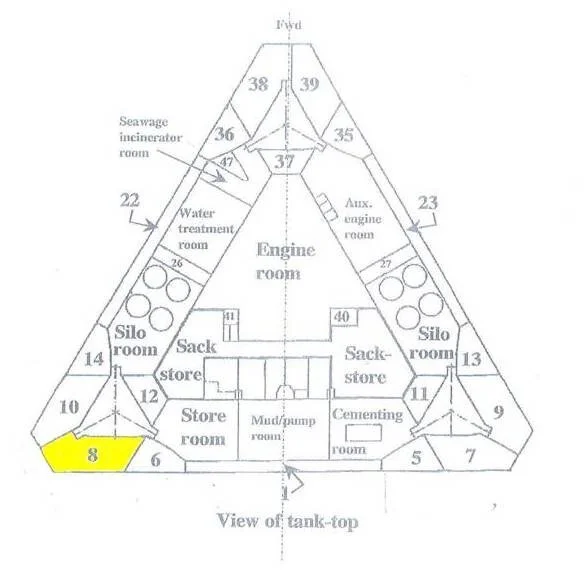
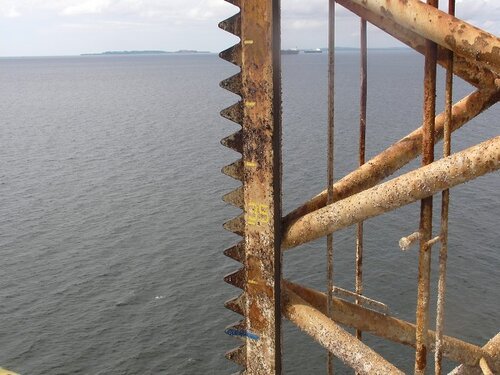
Legs before coatings
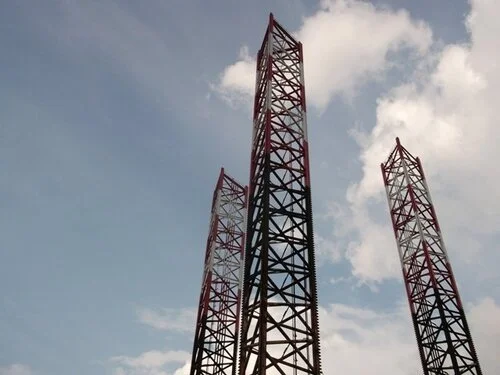
Legs after coatings
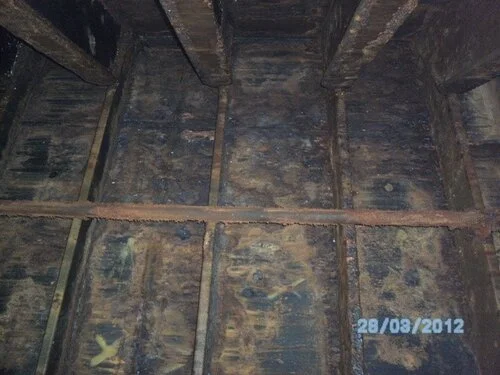
Pre-load tank before repair
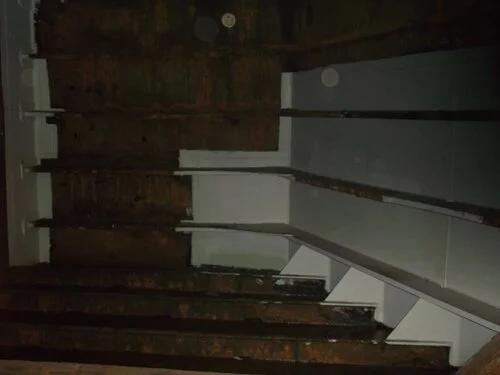
Pre-load tank after repair
After repair and ready to work
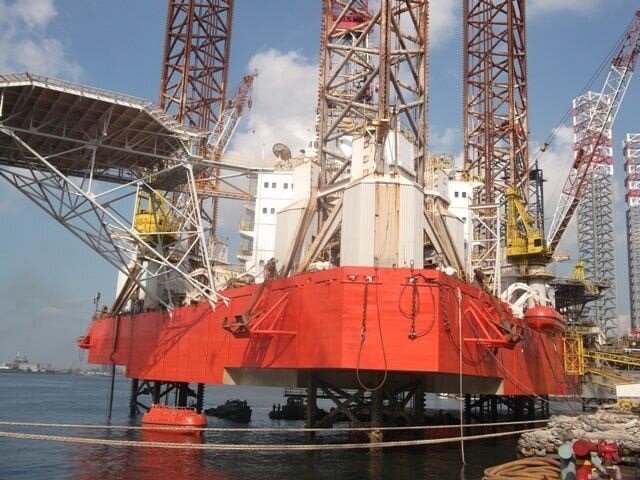
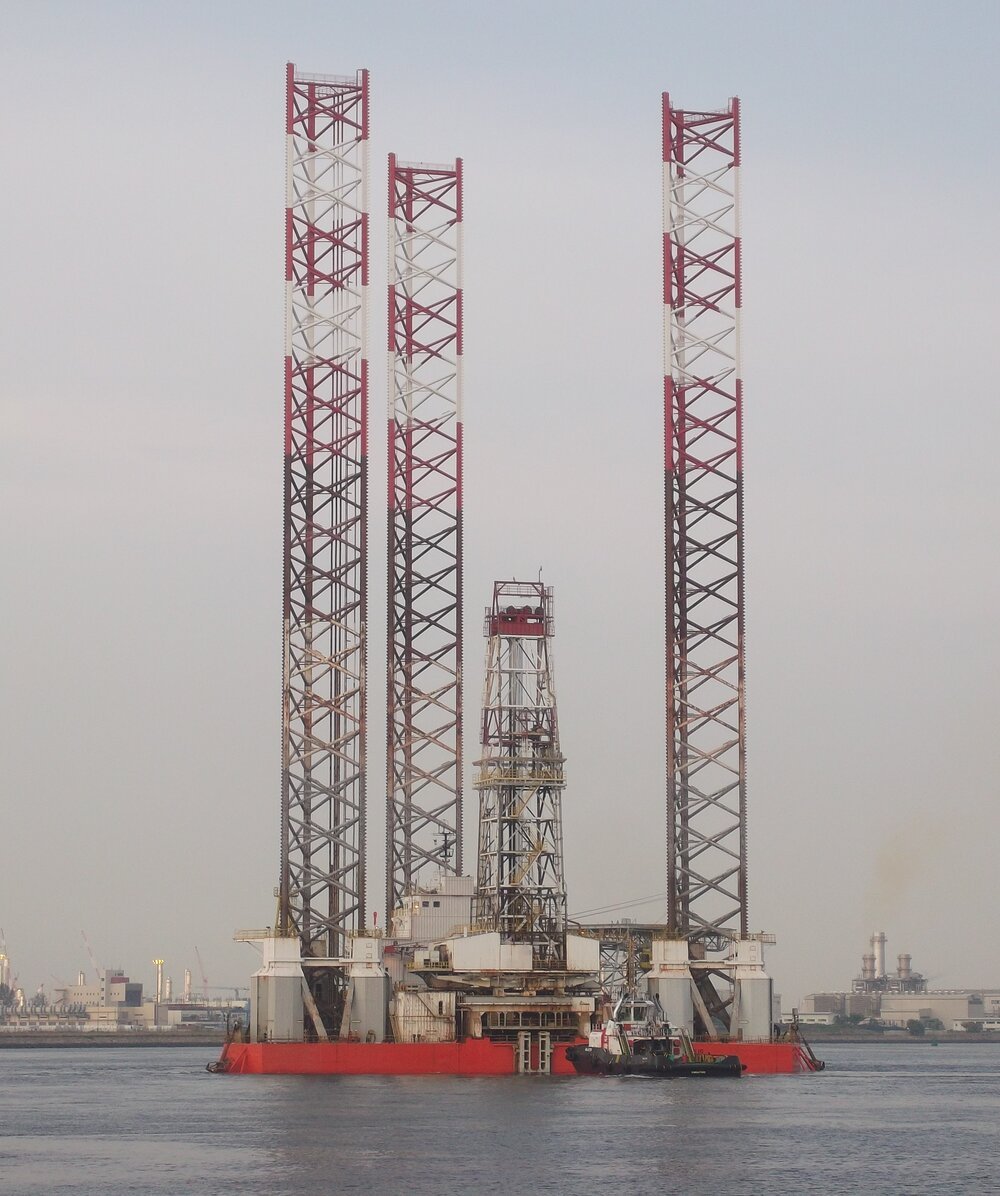